coilCAM

Samuelle Bourgault, Pilar Wiley, Avi Farber, and Jennifer Jacobs. 2023. CoilCAM: Enabling Parametric Design for Clay 3D Printing Through an Action-Oriented Toolpath Programming System. CHI 2023, Hamburg, Germany. doi: https: //doi.org/10.1145/3544548.3580745 ︎ Best Paper Honorable Mention
Clay 3D printing provides the benefits of digital fabrication automation and reconfigurability through a method that evokes manual clay coiling. Existing design technologies for clay 3D printing reflect the general 3D printing workflow in which solid forms are designed in CAD and then converted to a toolpath. In contrast, in hand-coiling, form is determined by the actions taken by the artist’s hands through space in response to the material. We theorize that an action-oriented approach for clay 3D printing could allow creators to design digital fabrication toolpaths that reflect clay material properties. We present CoilCAM, a domain-specific CAM programming system that supports the integrated generation of parametric forms and surface textures through mathematically defined toolpath operations. We developed CoilCAM in collaboration with ceramics professionals and evaluated CoilCAM’s relevance to manual ceramics by reinterpreting hand-made ceramic vessels. This process revealed the importance of iterative variation and embodied experience in action-oriented workflows.
This work is part of my Ph.D. in Media Arts and Technology at the Univeristy of Califronia, Santa Barbara in the Expressive Computation Lab. In Collaboration with Pilar Wiley, Avi Farber and Jennifer Jacobs.
Downloadable library at coilCAM.com. Downloadable paper on the ECL website.
Presented at
CoilCAM is programming system that supports the design of mathematically-defined toolpath operations for clay 3D printing. We built our system using custom Grasshopper Python Script components.

For sake of clarity (and aesthetic!), we use color-coded nodes to visualize CoilCAM’s components.

Our system is designed around the toolpath unit generator (TUG), which offers four shaping parameters: radius, scale, rotate and translate. By default, the TUG consists of a cylindrical toolpath. However, this default toolpath can be modified by modulating the shaping parameters.
To modulate the TUG’s shaping parameters, the system offers currently five function operators: linear, sinusoidal, square wave, staircase and exponential. By chaining these function blocks together, a craftsperson can create increasingly complex functions. The system also implements two Boolean operators: union and difference. These Boolean operations are done at the level of the toolpath which ensures that the desin can be fabricated.

Since the system is parametric, CoilCAM enables craftspeople to work through rapid and emergent variations. The following figure shows how we designed a functional pitcher starting from a default cylindrical toolpath.
CoilCAM’s low-level control over toolpath operations enables skilled craftspeople to plan for collaborative opportunities with the 3D printer and clay during fabrication. In this sample teapot, the craftsperson uses a tool or a finger to guide and support a gravity-shaped handle in real-time.

CoilCAM's representation of machine actions enabled craftspeople to plan for manual modifications such as part assembly of 3D-printed clay artifacts.

We also created many artifacts to demonstrate the wide range of forms and textures that CoilCAM enables. We identifed design patterns available through the use continuous and discrete-like function operators. Continuous function operators (linear, sinusoidal) appeared to be particularly useful for designing forms, while discrete-like function operators (square wave and staircase) served well to create intricate surface textures. The following tea set shows how CoilCAM enables the design of non-cylindrical forms (the teapot), parametric variations (matching but unidentical teacups) and intricate textures (the planter).

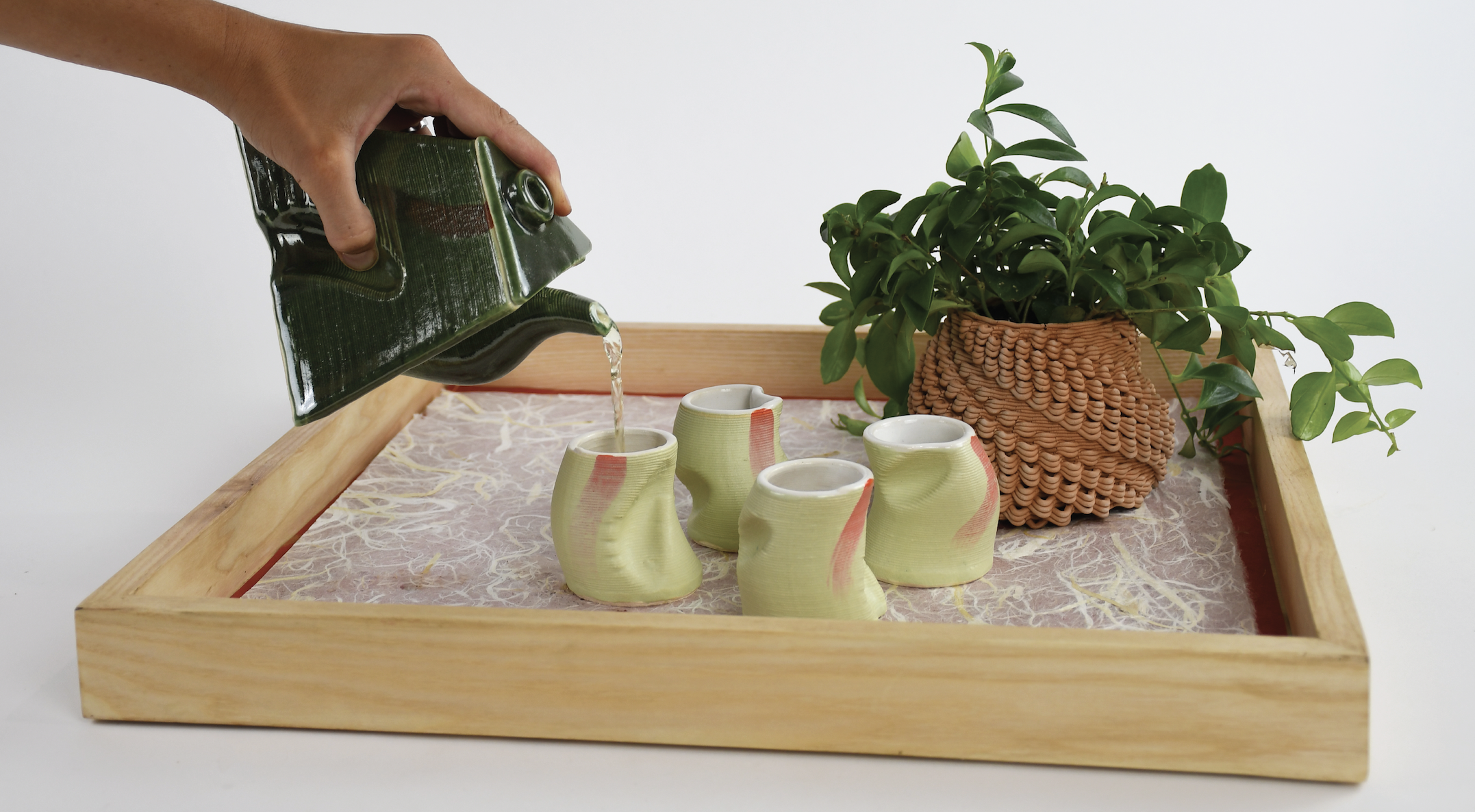
And some more stuff!

c::