Vitrified Sounds
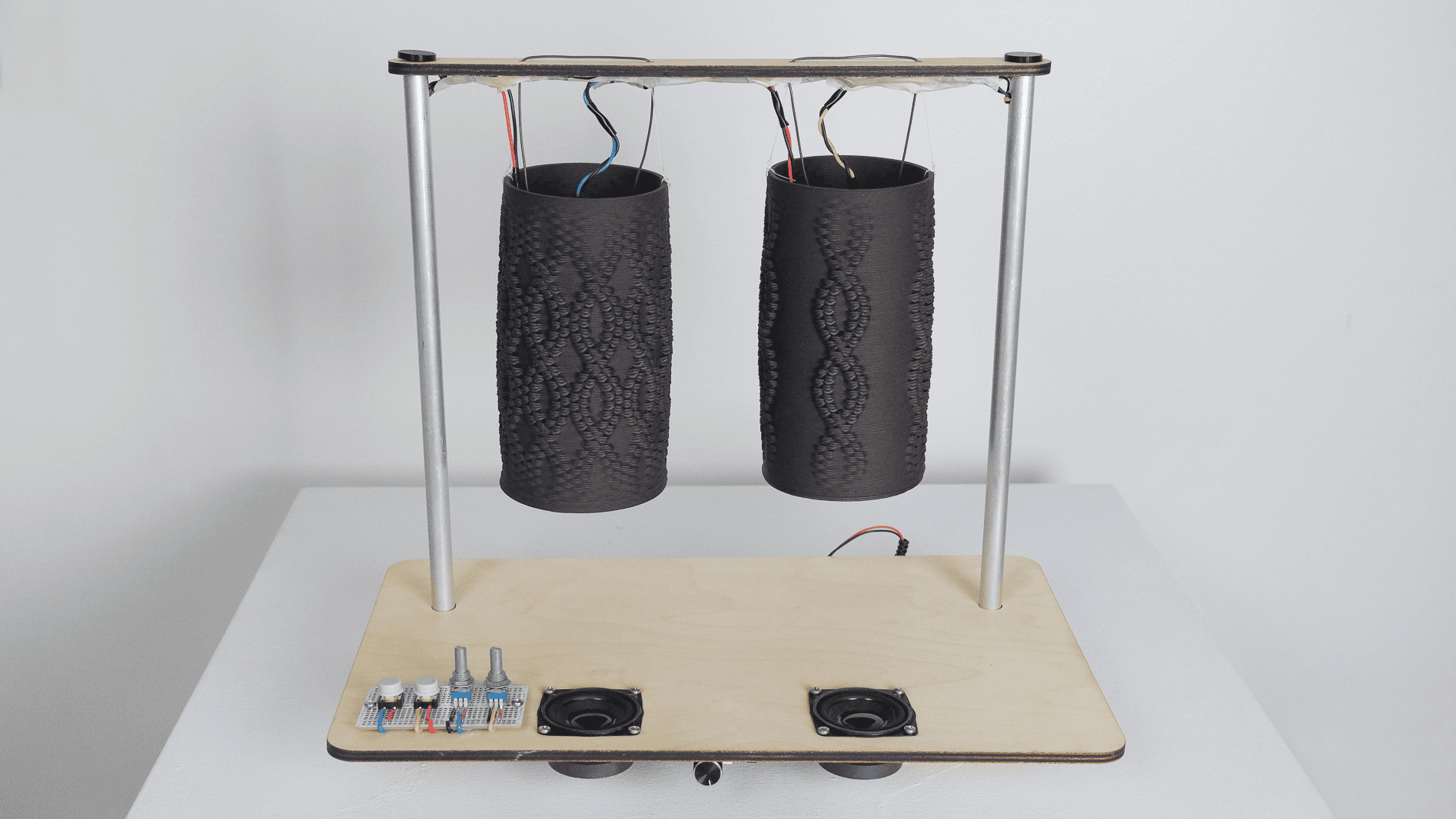
3D printed ceramic vessels, electronics, Teesny, motors, speakers, wood, metal rod. 2024.
Pottery practices stretch back to early human civilizations. While the technology we use to fabricate with clay has evolved, the process through which it vitrifies remains the same. The crystalline structure of ceramic provides both strength and beauty. As an ode to this ubiquitous material that transcends human experience, we augment two 3D-printed clay vessels with electronic components. We process the physical sound of these vessels being struck by motors through systems of oscillators, which, like groups of fireflies, exhibit coupling behavior. This is The Vitrified Sounds Instrument.
The Vitrified Sounds Instrument processes the ringing of clay 3D printed vessels struck by motors. The motors run using pulse width modulation from a Daisy board and are amplified by a transistor circuit. As they struck the vessels, piezo mics installed on the ceramic surface record ringing into delay lines that are resampled at varying times to be fed into an amplifier assembly. The signal is sent to the Daisy board for processing. Free-running accumulators sequence 8 overtones, four per vessel, which are synthesized. Knobs allow interactive control of delay times and speed of the sequencers through the Daisy. All processing is done in the gen environment inside of Max. After processing, the final audio outputs from both channels are fed to a final amplifier, which drives the speakers.
A project made with Jazer Sibley-Schwartz, Devon Frost, and Marcel Rodriguez-Riccelli for the synthUX Hackathon 2024.
Presented at
First Thursday, Santa Barbara, CA, USA
c::